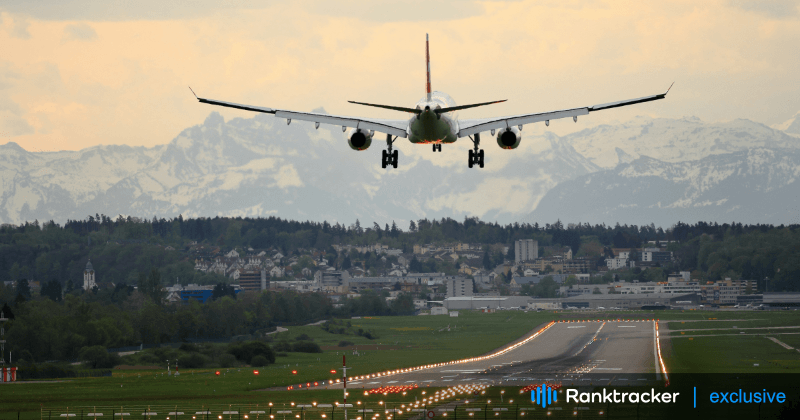
Intro
In the competitive landscape of contemporary manufacturing, efficiency is not just advantageous—it's absolutely crucial. As manufacturers are perpetually compelled to evolve, streamline, and refine their processes to meet the relentless demands of the market, the concept of Line Balance Optimization emerges as a linchpin strategy for operational excellence. This comprehensive exploration delves into the intricacies of line balancing, underscoring its significance, methodologies, challenges, and the transformative impact it holds for manufacturing efficiency.
Understanding Line Balance in Manufacturing
The manufacturing sector has always been the bedrock of economic progress, innovation, and industrialization. Yet, in this epoch of globalization and technological advancements, manufacturing entities face an untold pressure to elevate their efficiency metrics. Efficiency, in this realm, transcends mere productivity; it encapsulates the reduction of waste, optimization of resources, and maximization of outputs—all while maintaining quality and sustainability. It is within this context that line balance optimization emerges as a strategic beacon, guiding manufacturing operations towards unprecedented levels of efficiency and productivity.
Line balancing, in the realm of manufacturing, pertains to the equitable distribution of workload across all stages of the production process. The essence of line balancing is to ensure that each station or phase in the production line receives an optimal load, preventing any singular point from being overburdened or underutilized. This strategic distribution is pivotal for harmonizing the flow of operations, reducing wait times between processes, and notably, curtailing the occurrence of bottlenecks.
How Line Balance Impacts Manufacturing Efficiency
The impact of excellent line balancing on the efficiency of manufacturing is overpowering and complex. Firstly, line balancing enables uninterrupted, continuous production, thereby freeing up all resources as much as possible – both human and mechanical – and, at the same time, reducing unnecessary ones. Secondly, this enshrining of production processes allows for a sharp increase in production volumes, as well as an increase in the quality of work performed – as a result, productivity will increase, and, consequently, profitability.
The Consequences of Poor Line Balancing
Overview of Common Issues like Bottlenecks and Idle Time
Ill-balanced production lines are the progenitors of numerous operational inefficiencies, notably bottlenecks—where the congested flow of operations leads to delays and accumulates backlog—and excessive idle time, where resources are underutilized. These inefficiencies are not merely operational hiccups; they represent substantive leaks in productivity and resource utilization.
Impact on Productivity and Profitability
The ramifications of poor line balancing extend beyond the operational sphere into the domains of productivity and profitability. Bottlenecks elongate production times and escalate costs, while idle time squanders valuable resources. These inefficiencies concomitantly deteriorate product quality and delay delivery schedules, tarnishing the manufacturer’s reputation and compromising competitive advantage.
Principles of Line Balance Optimization
Key Principles for Achieving Optimal Line Balance
Achieving an optimal line balance is predicated on a meticulous understanding of the production process, comprehensive timing of each task, and strategic task allocation to minimize bottlenecks and idle time. This endeavor necessitates a keen analysis of process flows, time studies, and a relentless pursuit of process improvement.
Principles’ Role of These Principles in Improving Efficiency
The principles’ application will play a significant role in providing a structured way process, optimal resource utilization, and considerably reducing waste. Closer alignment of production processes to the ideal, manufacturers are guaranteed substantial improvements in efficiency and productivity that would amplify their performance trends and competitive advantage.
The Benefits of Optimized Line Balancing
Optimized line balancing is not merely an operational strategy; it's a transformative force that redefines the manufacturing landscape. The benefits are manifold:
- Improved Production Rates: Seamless operation flows lead to faster production cycles and increased output volumes.
- Reduced Labor Costs and Increased Profitability: Efficient allocation of human resources reduces overtime and operational costs, thus enhancing the bottom line.
- Better Product Flow and Reduced Production Time: A well-tuned production line facilitates a smoother product journey from inception to completion, curbing production times and enabling timely deliveries.
Assessing Your Current Line Balance
To embark on optimization, it’s imperative to assess the existing state of your production line. This evaluation entails a granular analysis of each process segment, identifying bottlenecks, and gauging the efficiency of current workflows. Recognizing areas of inefficiency is a critical step towards impactful improvement.
Strategies for Effective Line Balancing
Optimizing line balance can be achieved through diverse strategies, including task reallocation, workstation redesign, or technology integration, tailored to suit specific operational contexts. Demonstrable success in line balancing often arises from a bespoke blend of these strategies, diligently applied in concert.
Implementing Changes and Overcoming Challenges
However, as pointed out, change is a powerful factor that may provoke a resistance reaction. The move to optimized line balance should focus on planning and proper communication of the next steps to minimize damage. The ability to overcome change-based challenges plays a central role in maintaining stakeholder adoption and successful adjustments to new streams of business.
The Contribution of Technology and Line Balancing Software
With no doubt, technology plays a key role in optimized line balance nowadays. Uhline.com states, “line balancing software has state-of-the-art analytical tools that can help you analyze the current process, identify any inefficiencies, and simulate a change to make an evidence-based decision”.
**Helpful analytics, process modeling, and optimization simulation **
Digital production line balance platforms like LineView can help ensure decision making is data-driven and always based on the most current information.
Benefits of software use: Improved accuracy and analysis speed and the ability to continuously push for improvement due to increased ease of Line balance optimization case studies: lessons in line success
Conclusion
The path to maximum manufacturing efficiency entails an inappropriate pursuit of perfect line balance. The profound, yet straightforward approach is the answer to achieving unprecedented levels of productivity, sustainability, and competitiveness. All manufacturers who are not afraid to implement the optimization of line balance, apply the leading-edge technology, and overcome numerous related obstacles may shed the potential of drastic growth. The path to optimized line balance is still infinite, yet it is a path every mindful manufacturer should take for a greater future of manufacturing perfection.